.png)
BUILDINGS, GROUNDS AND EQUIPMENT
The layout of our premises and equipment has been designed to:
1. meet GMP Regulatory requirements
2. allow effective cleaning and maintenance to take place
3. avoid cross-contamination and the build up of dust or dirt and any other adverse effect on the quality of products.
4. protect against the entry of insects and other pests/rodents.
However, we rely on you to help us maintain the high standards of our premises and equipment to ensure that GMP requirements are met at all times.
Follow the steps below to ensure that the quality of premises and equipment are not adversely affected.
Step 1 – Conduct all work in such a manner that avoids causing contamination of materials or products.
Step 2 – Prevent the entry of any unauthorised person into the production, storage and quality control areas.
Step 3 – Perform cleaning activities of the premises and equipment in accordance with written procedures.
Step 4 – Store tools and parts in rooms or lockers reserved for that purpose.
Step 5 – Tag out defective equipment and remove it the work area.
Step 6 – Do not use processing and packaging areas as thoroughfares and storage areas and keep doors closed when rooms are not in use.
DOCUMENTATION
Good documentation is another principle of GMP. Documentation provides essential information and procedures that when followed, helps to minimise mistakes and errors. Pharmaceuticals manufacturers have a range of documentation, including but not limited to:
1. Specifications
2. Master batch hand packaging instructions
3. Standard Operating Procedures (SOP), Operating Instructions (OI), Forms, Logs, Registers
4. Test methods, testing records
Employee should always perform their duties in accordance with the relevant documentation.
All master documents have unique document numbers and unique titles for identification and must be:
1. Signed at the bottom of the first page by the document r
2. Authorised by department manager and QA manager
3. Controlled and distributed with care
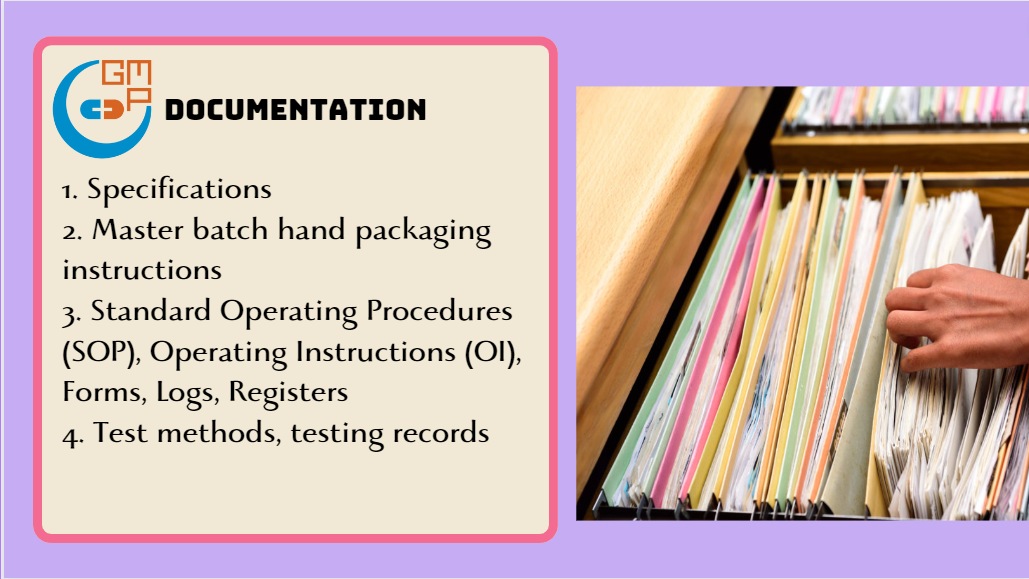
Specifications:
Following are few types of specifications used by Pharmaceuticals manufacturer:
1. Packaging – labels, leaflets, cartons, shippers and inserts etc.
2. Components – bottles, caps, pillow packs, vials, applicators etc.
3. Raw materials and consumables – chemical and biological materials and cleaning reagents
4. Processing aids – filters, blue wrap, silicon tubing, clamps, kegs, carboys, bottles and aspirators
5. Finished products – all finished products manufactured on site and any product where a part of the manufacturing process is conducted by a third party
Master Batch and Packaging Instructions:
Master Batch records for each product and batch size manufactured, tested, packed and labelled:
1. Antigen production
2. Vaccine production
3. Pharmaceutical production
4. Secondary packaging products
SOP’s, OI’s, Logs and Forms:
Following are some examples of written procedures and associated records including but not limited to:
1. Receiving deliveries of materials
2. The labelling, quarantining and storage of materials
3. Sampling and testing of materials and products
4. Release and rejection
5. Batch processing and packaging
6. Validation
7. Equipment assembly and calibration practices
8. Maintenance, cleaning and sanitisation
9. Personnel matters including training, clothing, hygiene
10. Environmental monitoring
11. Pest control
12. Complaints, recalls and returns
13. Supplier management
14. Internal audits
Test Methods and Test Records:
Test methods and test records describe the categories of products manufactured and the parameters and testing of each of the product categories. Inspection and reporting of results are described for each area of testing including but limited to:
1. Sterility
2. Microbiology
3. Immunology
4. Chemistry – pharmaceutical and biological
COMPLETING RECORDS
When completing an entry on a record or document, employees should always ensure that:
1. The form or document used is the current version
2. Complete the entry in real time – backdating entries or signatures is prohibited
3. The entry recorded is accurate
4. Handwriting is legible
5. Only use blue or black pen
The use of correction tape or liquid paper is prohibited. If an entry needs to be altered on a document, follow the process:
1. Draw a line through the error and initial and date the correction next to the corrected entry
2. Ensure that the correction allows the original information to be read
3. If the change is not obvious, record the reason for the alteration
4. Always cross out the full number/word or date rather than the individual digit/letter when making a correction
Important:
Signature and initial on a document are part of identity. This means that staffs are responsible for anything they have signed or initialled. If unsure about, or don’t understand the details of a document, staffs should speak to your manager before signing. Never sign or initial if you don’t understand!
PRODUCTION PROCEDURE
GMP outlines the requirements for every stage in the production process of pharmaceutical goods. Organisation’s procedural documents outline these processes. Employee must ensure that they handle materials at all stages of production, in accordance with these procedures. If any staff identify any damaged containers and/or other problems that might affect the quality of a material, they should immediately report the matter to your Supervisor / Manager.
1. Please ensure following good practices are followed all the time.
2. Production processes must be conducted in a way to minimise the risk of cross-contamination
3. Production processes must be validated to ensure that they are achieving the desired result
4. Starting materials must be purchased, received and dispensed in a manner that minimises risk
5. Processing operations must occur in clean, tidy and well-maintained work areas
6. Packaging materials must be purchased, handled and controlled in a manner that minimises the risk of contamination
7. Packaging operations must minimise the risk of cross-contamination, mix-ups and substitutions
8. Finished products must be stored and evaluated correctly before and during release
9. Rejected, recovered and returned materials must be managed according to their level of risk

GMPc Vietnam is recognized throughout Vietnam as the leader in providing turnkey consulting solutions for GMP-certified facility projects, including Pharmaceuticals, Cosmetics, Health supplements and Veterinary pharmaceutical. Though 12 years of development 2011 to 2023, GMPc has implemented more than 230 GMP-certified facility projects, equaling to more than 80% of market share of the field in Vietnam. Not only do domestic customers, foreign investors also choose GMPc as their consultant when investing new factories in Vietnam, such as Kyoto Biken Vaccine Factory, Nippon Chemiphar Pharmaceutical Factory, Shimizu Contractor, Kajima Contractor, etc.
Consulting services for EU GMP
Consulting services by GMPc Vietnam
GMP project consulted by GMPc Vietnam