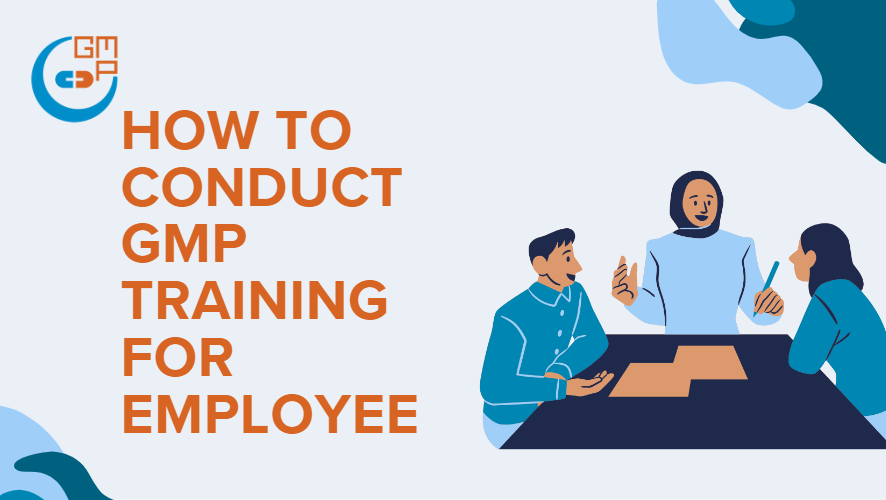
A successful GMP training for employee ensures that all staff will receive adequate, relevant and documented training to enable them to perform their assigned functions safely and in compliance with applicable guidelines/regulations.
It is a GMP/GLP requirement that all personnel be trained in the work appropriate to their role. FDA regulated industries should prepare GMP Training policies and procedures for their employees outlining training approaches, scope, responsibilities and overall training system. There should be clear process to establish training needs, provide trainings, evaluate, record, reward archive as required by the local regulatory authorities.
Types of GMP trainings for employees
GMP regulated businesses carefully determine what type of training is practical and reasonable for their staff. Following is a list of common GMP training that most GMP sites are accustomed:
- Induction training
- Skills training
- Good Manufacturing Practices (GMP) training
- Good Laboratory Practices (GLP) training
- Quarantine requirement training
- Gowning qualification training
- Work, Health and Safety training
- External certification training
- Permit to Work systems
- Personal Protective Equipment (PPE)
- Bio-Security
- Permit to Work systems
- Auditor training
- Hazard/Incident Reporting and Investigation
Out of the above trainings, induction, skill and Work, Health & Safety trainings are applied to all employees, contractors (including cleaning staff) and casual staff.
GMP/GLP and PPE trainings are applied to all employees, contractors and casual staff working in a GMP environment that includes manufacturing, packaging, labeling, distribution, QA, QC, development, validation, engineering, IT staff and anyone whose activities could affect product quality.
Gowning qualification training applies to all staff working in cleanroom processing areas on top of the training regime mentioned above.
Quarantine and bio-security training are applicable to employees working in biological processing sites. Permit to Work training is required for engineering and project staff.
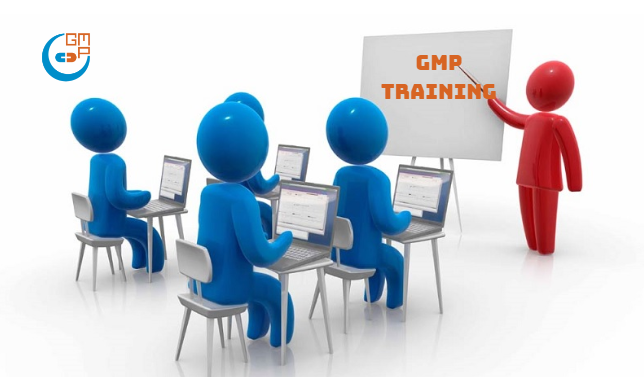
Responsibilities for a successful GMP training program
A GMP training for employee program should start at the top of an organization and flow directly to the bottom. It can be effective to create a training task force or individual with support senior management, who coordinates training and is responsible for its implementation.
Employees:
All employees and contractors are responsible to:
– Know their training requirements.
– Actively participate in training and assessment and inform the trainer if they do not understand any of the material.
– Sign a training record indicating that they believe they are competent to conduct the work they have been trained in, or (where the training is knowledge training) that they understand the material they have been trained in.
– Discuss their individual training and development needs with their supervisor and/or manager in the first instance. Employees may request initial information the human resources department.
– Carry out agreed development plans.
– Maintain a copy of their training records in their work area – in the folder provided by the training system administrator.
Quality Assurance Manager:
Typically, the QA Manager is responsible to approve the design and implementation of the training system in collaboration with the human resources department. The role is responsible to ensure that:
– The Training System is GxP compliant.
– System reporting complies with KPI requirements for the business.
– The training system is audited annually.
– Approves the GMP/GLP training schedule and training plans for each role.
Work, Health and Safety:
The WH&S manager or specialist proposes and conduct a safety and environment training program that meets the WH&S and Environment compliance requirements as regulated by the local authorities. The team maintains records of all safety and environment related training.
Department Managers and Supervisors:
Department Managers and Supervisors are responsible for:
– Employees are trained in the work of their role in an agreed timeframe. This includes training of staff who are filling a role in a temporary capacity.
– New employees and contractors undergo GMP induction training within the first week of employment.
– Contractors undergo induction and other training relevant to their role in a timely manner.
– Training requirements for each role are identified, documented, approved and kept current.
– A plan is in place to ensure that training and development requirements for each employee (and contractor, where appropriate) are met on time.
Training Administrator:
The Training Administrator is responsible to:
– Ensure that training matrices and records are kept current, secure and accessible. This includes ensuring that references to the version of a given document aligns with the corresponding entry on the Controlled Document Index.
– Report training progress to managers, supervisors and employees.
– Ensure hard copy training records, accreditation certificates, and GMP training certificates are retained and appropriately d.
– Maintain a current list of trained and accredited staff.
– Audit the system periodically to ensure it complies with the company procedure.
– Provide supervisors/managers with draft training matrices and training plans for new roles.
– Provide monthly training status reports to the business.
Human Resource Manager:
The HR Manager is responsible to:
– Provide assistance to management in planning, coordinating and implementing relevant, cost effective training and development activities for all non QA, GMP and WH&S related training.
– Notify the training administrator of all new staff appointments and cessation of employment. This includes permanent and casual staff.
– Forward induction program information and records (includes GMP and safety induction) to a new employee’s manager at commencement of employment.
– Archive the completed training into employee’s personal s. Archive the training record for defined period after the employee has separated business.
GMP Trainers:
GMP Trainers are responsible to:
– Deliver the trainings in the most effective manner.
– Ensure that at the conclusion of training, training records are signed – by each trainee and the trainer.
– Forward the original training record to Training Administrator for record keeping and archiving.

GMPc Vietnam is recognized throughout Vietnam as the leader in providing turnkey consulting solutions for GMP-certified facility projects, including Pharmaceuticals, Cosmetics, Health supplements and Veterinary pharmaceutical. Though 12 years of development 2011 to 2023, GMPc has implemented more than 230 GMP-certified facility projects, equaling to more than 80% of market share of the field in Vietnam. Not only do domestic customers, foreign investors also choose GMPc as their consultant when investing new factories in Vietnam, such as Kyoto Biken Vaccine Factory, Nippon Chemiphar Pharmaceutical Factory, Shimizu Contractor, Kajima Contractor, etc.
Consulting services for EU GMP
Consulting services by GMPc Vietnam
GMP project consulted by GMPc Vietnam