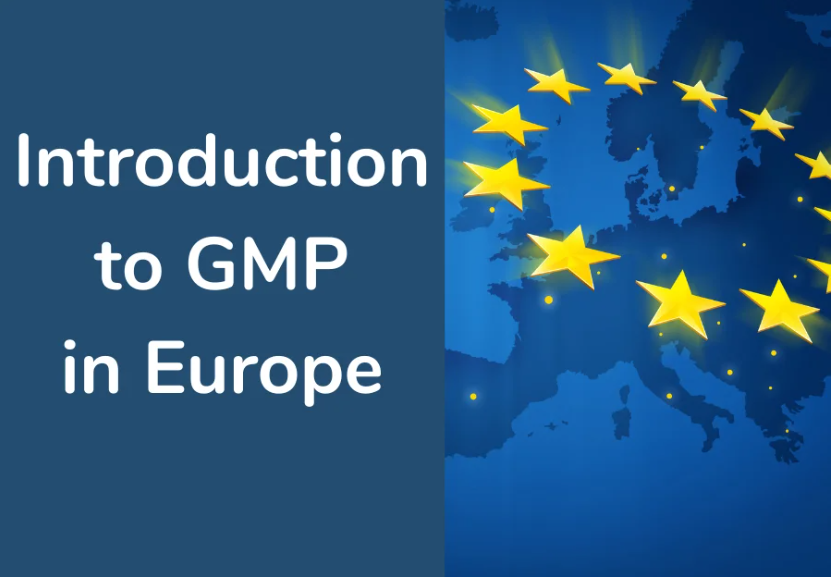
The quality of pharmaceuticals has been a concern of the World Health Organization (WHO) since its inception. The setting of global standards is requested in Article 2 of the WHO Constitution, which cites as one of the Organization’s functions that it should “develop, establish and promote international standards with respect to food, biological, pharmaceutical and similar products.”
The first GMP text published by WHO was developed during 1967-69 upon request by WHO’s Member States and was revised in 1975.
Revised and expanded GMP guidelines were prepared during 1989-90, approved by the WHO Expert
Committee on Specifications for Pharmaceutical Preparations in late 1990 and subsequently published by WHO. At that time, Part One of these revised and expanded guidelines set out the philosophy and essential elements of GMP; Part Two dealt with good practices in production and quality control. These two parts together represented the “core” of the GMP guidelines published by WHO.
The EU and WHO guidelines are based on the same principles but differ in detail.

Premises and equipment
These requirements on “Premises and equipment” aim at ensuring an adequate construction of rooms and equipment to guarantee:
• suitability for the provisioned work tasks,
• minimizing the failure risk,
• easy to clean and maintain.
They therefore aim at avoiding cross-contamination and further possibilities of impairing the product quality.
Formally seen the EU guidelines state the requirements regarding premises and equipment within one chapter (chapter 3). The WHO guidelines divide this topic into chapter 12 “Premises” and Chapter 13
“Equipment”.
The content relating to the prerequisits regarding:
• Production areas,
• Weighing areas,
• Storage areas,
• Quality control areas,
• Ancillary areas,
• Manufacturing equipment,
• Washing and cleaning equipment,
• Balances and measuring equipment,
• Pipework, etc.
is the same.
As before, the WHO guidelines are also on this topic partly more detailed and list not only the requirements e.g. “Production areas should be regularly monitored during both production and nonproduction periods …” but as well the activities which have to be carried out to demonstrate that the requirements will be fulfilled.
Moreover, there are further WHO documents regarding the topic “Equipment”, e.g.:
• the WHO workout “WHO good manufacturing practices: starting materials”4 or
• WHO guidelines on transfer of technology in pharmaceutical manufacturing”5 and
• others.

GMPc Vietnam is recognized throughout Vietnam as the leader in providing turnkey consulting solutions for GMP-certified facility projects, including Pharmaceuticals, Cosmetics, Health supplements and Veterinary pharmaceutical. Though 12 years of development 2011 to 2023, GMPc has implemented more than 230 GMP-certified facility projects, equaling to more than 80% of market share of the field in Vietnam. Not only do domestic customers, foreign investors also choose GMPc as their consultant when investing new factories in Vietnam, such as Kyoto Biken Vaccine Factory, Nippon Chemiphar Pharmaceutical Factory, Shimizu Contractor, Kajima Contractor, etc.
Consulting services for EU GMP
Consulting services by GMPc Vietnam
GMP project consulted by GMPc Vietnam