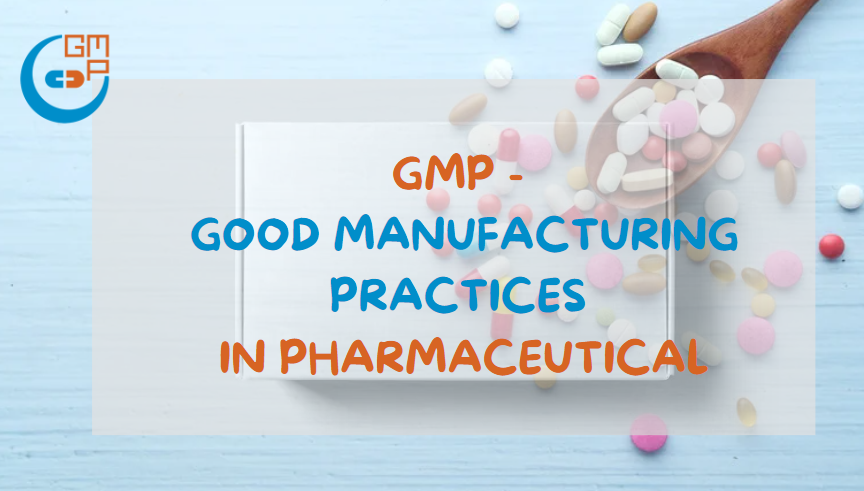
What is Good Manufacturing Practices?
+ GMP stands for Good Manufacturing Practices
+ There are several guidelines for good manufacturing practices worldwide but GMP guidelines provided by WHO and FDA are followed worldwide
+ Recommendations on manufacturing, quality control, storage, and distribution
+ Good Manufacturing Practices in pharmaceutical has 14 components
Components of GMP
1. Quality Management System
• Outlines the processes, procedures, and responsibilities necessary to achieve and maintain GMP compliance
• It encompasses the establishment of quality objectives, documentation control, change control, deviation management, and the handling of quality-related incidents
• Ensure that all manufacturing activities are carried out in a controlled and consistent manner
2. Personnel
• Ensure that all individuals involved in the manufacturing process are appropriately trained, qualified, and competent for their respective roles
• It includes documented job descriptions, training programs, and competency assessments
3. Facilities and Equipment
• Facilities and equipment must meet specific GMP requirements to ensure the safety, quality, and integrity of the manufacturing process
• Suitable manufacturing areas, storage areas, and utilities such as HVAC systems, water purification systems, and cleanrooms
• Equipment should be designed, installed, and maintained to prevent contamination, facilitate cleaning, and operate effectively
4. Sanitation and Hygiene
• Maintaining a clean and hygienic manufacturing environment is essential for GMP compliance
• Regular cleaning and sanitization of facilities and equipment, appropriate waste disposal procedures, and the implementation of hygiene practices for personnel
5. Documentation and Record-keeping
• Accurate and complete documentation is a critical component of GMP
• This includes the creation, review, approval, and control of various documents
• Ensure all relevant data, including raw material information, equipment logs, and quality control results, are recorded and retained appropriately
6. Raw Materials and Components
• Establish procedures for their receipt, inspection, sampling, and storage to ensure their identity, quality, and suitability for use
• Adequate controls should be in place to prevent cross-contamination and mix-ups
7. Production Process
• GMP requires a well-defined and controlled production process
• This includes process validation to demonstrate that the manufacturing process consistently produces products meeting quality specifications
• Any deviations or out-of-specification results should be investigated and appropriately addressed
8. Packaging and Labeling
• Packaging materials should be of suitable quality, compatible with the product, and adequately controlled
• The packaging process should be validated, and labeling activities should comply with regulatory requirements
• Ensure accurate and legible information about the product, its dosage, storage conditions, and any warnings or precautions
9. Quality Control
• It involves a range of testing and analysis activities
• This includes the testing of raw materials, in-process samples, finished products, and stability samples
• Quality control laboratories should be properly equipped, staffed with trained personnel, and follow validated test methods and procedures
10. Product Complaints and Recalls
• This includes monitoring and analyzing product complaints, investigating their root causes, and implementing CAPA as necessary
• Requires the implementation of a robust product recall system
• Documented product recall procedure including notification to regulatory authorities, retrieval of affected products the market, and appropriate communication with customers and stakeholders
11. Validation and Qualification
• Validation and qualification are important components of GMP to ensure that processes, systems, and equipment
• This includes process validation, equipment qualification, cleaning validation, and analytical method validation
• This involves establishing documented protocols, performing testing and analysis, and documenting the results
12. Change Control
• This is a crucial aspect of GMP to manage any changes that may impact product quality, safety, or efficacy
• This includes changes to processes, equipment, materials, facilities, or systems
• GMP requires a formal change control process
13. Audits and Inspections
• Internal audits are conducted by the company to assess its own adherence to GMP standards
• External inspections are performed by regulatory authorities to assess compliance with GMP regulations and guidelines
• These audits and inspections help to identify any non-compliance issues and ensure continuous improvenents
14. Training and Continuous Improvement
• Ensure that all personnel are trained on GMP principles, procedures, and practices relevant to their roles
• Regular training updates should be provided to keep employees informed about changes in regulations
• Continuous improvement initiatives help to enhance the overall quality

GMPc Vietnam is recognized throughout Vietnam as the leader in providing turnkey consulting solutions for GMP-certified facility projects, including Pharmaceuticals, Cosmetics, Health supplements and Veterinary pharmaceutical. Though 12 years of development 2011 to 2023, GMPc has implemented more than 230 GMP-certified facility projects, equaling to more than 80% of market share of the field in Vietnam. Not only do domestic customers, foreign investors also choose GMPc as their consultant when investing new factories in Vietnam, such as Kyoto Biken Vaccine Factory, Nippon Chemiphar Pharmaceutical Factory, Shimizu Contractor, Kajima Contractor, etc.
Consulting services for EU GMP
Consulting services by GMPc Vietnam
GMP project consulted by GMPc Vietnam