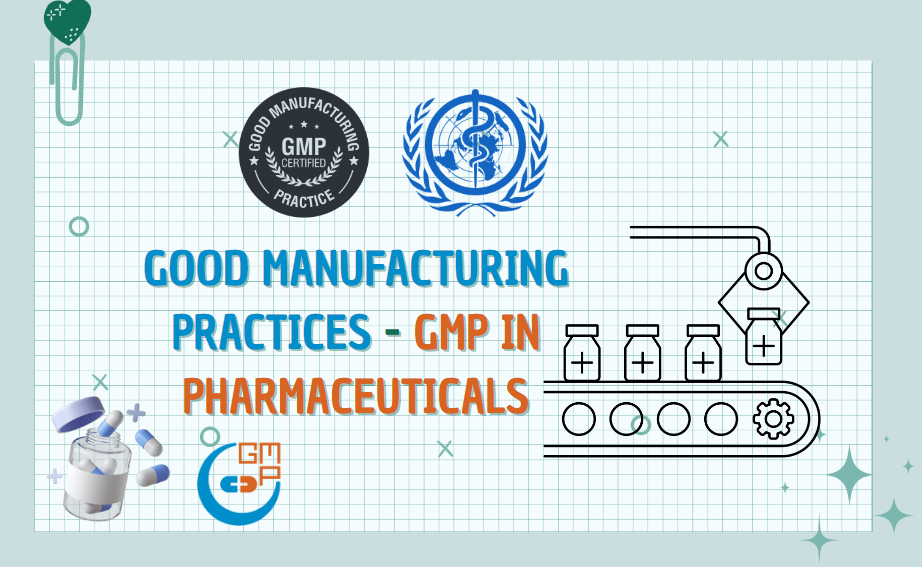
Good manufacturing practices are a group of guidelines those are regulated by WHO since 1975 throughout the world. The aim of GMP is to ensure the quality of the pharmaceutical products. Therefore, the GMP is considered as a quality seal for the pharmaceutical products.
The guidelines ensure the good production conditions in the production area and good testing of the product in quality control.
Many ries in the world adopted the GMP regulations provided by the WHO for their pharmaceutical production.
Some ries developed their own GMP guidelines for pharmaceuticals but the basic concept of all GMP guideline is to produce good quality medicines.
According to GMP guidelines if any pharmaceutical product passes all specified tests produced in GMP violating manufacturing area that should not be reached in the market.
The basic GMP facility requirements that have to be followed bu pharmaceutical manufacturers are:
- Manufacturing processes should be properly defined and controlled.
- All critical processes should be validated to ensure the consistency of the process.
- Results of the validation of the processes should comply with specifications.
- Batch Manufacturing Records should be controlled, and any changes to process should be evaluated.
- Changes that can have any impact on the quality of the product must be validated.
- Procedures and any instructions should be written in clear language to understand them properly.
- Personnel should be trained for production, quality control and to carry out the documentation.
- At the time of production and testing of final products, the records made manually or by instruments that provide the evidence that all the steps defined in procedures and instructions were done properly.
- Any deviation the written procedure should be investigated and documented.
- Documents of manufacturing including distribution with a complete history of batch should be retrained till the expiry the batch.
- A well-defined procedure should be available for recalling any batch the market. Market complaints of batches should be examined and the root causes of the defects should be investigated and appropriate preventive action should be taken to prevent recurrence of the defect.

GMPc Vietnam is recognized throughout Vietnam as the leader in providing turnkey consulting solutions for GMP-certified facility projects, including Pharmaceuticals, Cosmetics, Health supplements and Veterinary pharmaceutical. Though 12 years of development 2011 to 2023, GMPc has implemented more than 230 GMP-certified facility projects, equaling to more than 80% of market share of the field in Vietnam. Not only do domestic customers, foreign investors also choose GMPc as their consultant when investing new factories in Vietnam, such as Kyoto Biken Vaccine Factory, Nippon Chemiphar Pharmaceutical Factory, Shimizu Contractor, Kajima Contractor, etc.
Consulting services for EU GMP
Consulting services by GMPc Vietnam
GMP project consulted by GMPc Vietnam