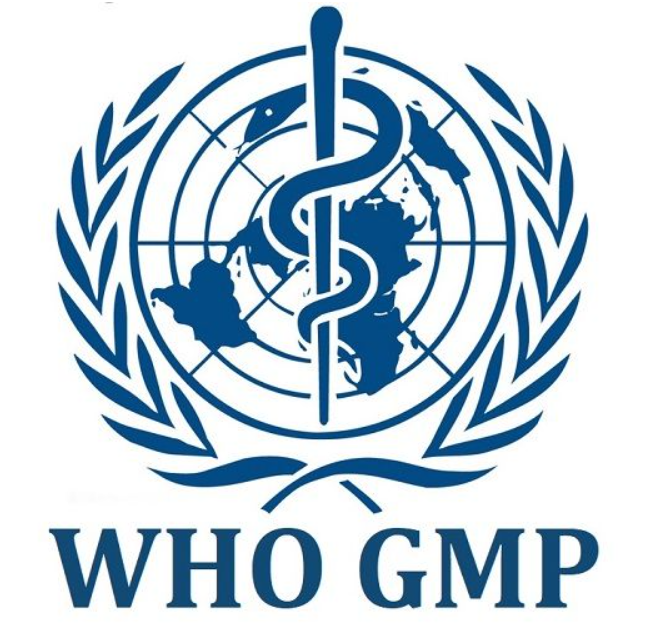
Good Manufacturing Practices (GMP, also referred to as 'cGMP' or 'current Good Manufacturing Practice') is the aspect of quality assurance that ensures that medicinal products are consistently produced and controlled to the quality standards appropriate to their intended use and as required by the product specification.
GMP defines quality measures for both production and quality control and defines general measures to ensure that processes necessary for production and testing are clearly defined, validated, reviewed, and documented, and that the personnel, premises and materials are suitable for the production of pharmaceuticals and biologicals including vaccines. GMP also has legal components, covering responsibilities for distribution, contract manufacturing and testing, and responses to product defects and complaints. Specific GMP requirements relevant to classes of products such as sterile pharmaceuticals or biological medicinal products are provided in a series of annexes to the general GMP requirements.
GMP guidance
The first WHO draft text on GMP was adopted in 1968. In 1969, when the World Health Assembly recommended the first version of the WHO Certification Scheme on the quality of pharmaceutical products moving in the global market, it accepted the WHO GMP as an integral part of the Scheme.
More than 100 ries have incorporated the WHO GMP provisions into their national medicines laws, and many more ries have adopted its provisions and approach in defining their own national GMP requirements. The WHO GMP continues to be used as a basis for the WHO Certification Scheme and prequalification of vaccines for procurement by UN agencies.
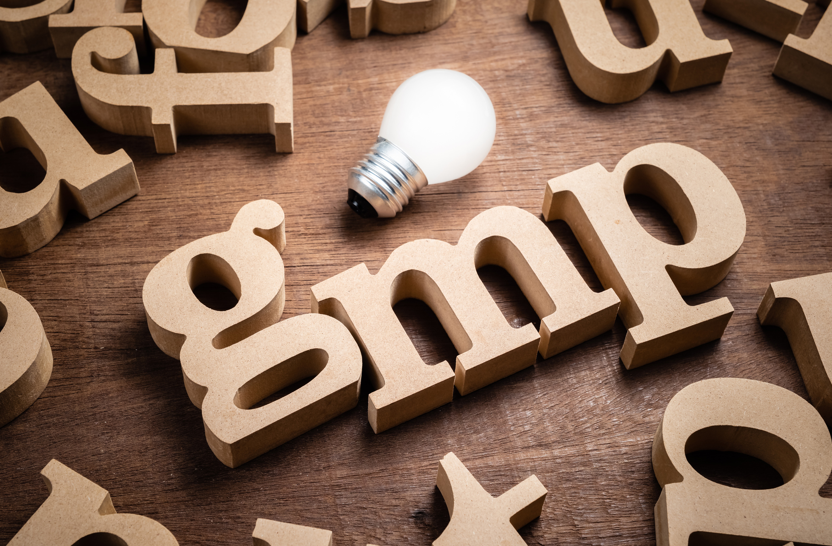
Why is GMP important?
Poor quality medicines are not only a health hazard, but a waste of money for both governments and individual consumers.
GMP helps boost pharmaceutical export opportunities. Most ries will only accept import and sale of medicines that have been manufactured to internationally recognized GMP. Governments seeking to promote their ries' export of pharmaceuticals can do so by making GMP mandatory for all pharmaceutical production and by training their inspectors in GMP requirements.
Good quality must be built in during the manufacturing process; it cannot be tested into the product afterwards. GMP prevents errors that cannot be eliminated through quality control of the finished product. Without GMP it is impossible to be sure that every unit of a medicine is of the same quality as the units of medicine tested in the laboratory.

GMPc Vietnam is recognized throughout Vietnam as the leader in providing turnkey consulting solutions for GMP-certified facility projects, including Pharmaceuticals, Cosmetics, Health supplements and Veterinary pharmaceutical. Though 12 years of development 2011 to 2023, GMPc has implemented more than 230 GMP-certified facility projects, equaling to more than 80% of market share of the field in Vietnam. Not only do domestic customers, foreign investors also choose GMPc as their consultant when investing new factories in Vietnam, such as Kyoto Biken Vaccine Factory, Nippon Chemiphar Pharmaceutical Factory, Shimizu Contractor, Kajima Contractor, etc.
Consulting services for EU GMP
Consulting services by GMPc Vietnam
GMP project consulted by GMPc Vietnam