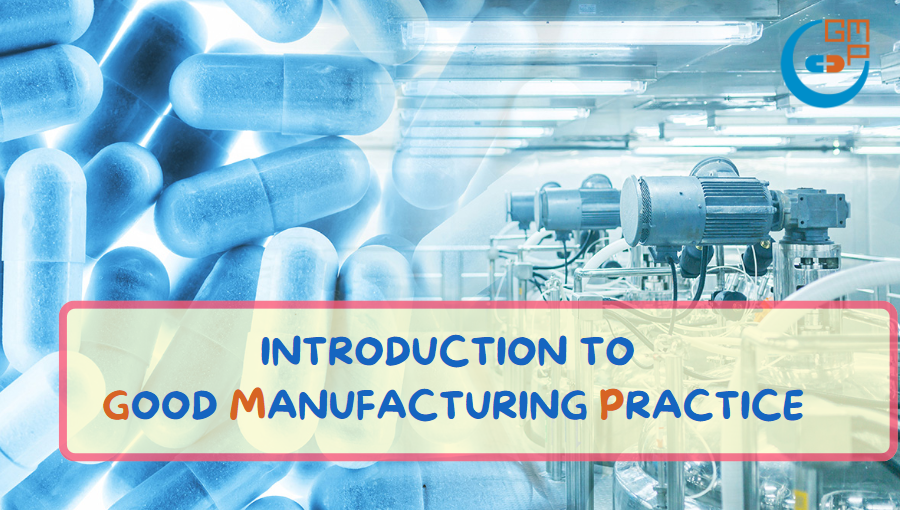
GMP is a set of principles and procedures that, when followed, helps to ensure that veterinary products are consistently manufactured to a high quality, are safe and in accordance with their registration particulars and specifications when they reach the target species.
GMP principles and procedures for Pharmaceutical products are outlined in the local regulatory agencies Acts and Legislations typically in the name of “Code of Good Manufacturing Practice”. This code covers all aspects of manufacturing, including:
1. QUALITY MANAGEMENT
2. PERSONNEL AND TRAINING
3. PERSONAL HYGIENE
4. BUILDINGS, GROUNDS AND EQUIPMENT
5. DOCUMENTATION
6. PRODUCTION
7. INTERNAL AUDITS
8. COMPLAINTS AND PRODUCT RECALLS
.png)
Pharmaceuticals manufacturers must ensure to apply the GMP guidelines, practices, quality and regulatory requirements detailed in the GMP code into their products in order to maintain their license to manufacture and distribution.
QUALITY MANAGEMENT
Quality management is a core principle of GMP as it is essential that all veterinary products are fit for their intended use and do not place target species at risk due to inadequate safety, quality, efficacy, purity or identity.
Quality management within GMP covers:
1. QUALITY ASSURANCE
2. QUALITY CONTROL
3. PRODUCT QUALITY REVIEWS
4. QUALITY RISK MANAGEMENT
Licensed Pharmaceuticals manufacturer has workers, equipment and facilities to ensure quality of all products they manufacture. However, they also rely on their employees to participate in quality objectives. Therefore, it is everybody’s responsibility to identify and report quality issues to management immediately.
1. QUALITY ASSURANCE:
Quality assurance operates at the process level to ensure manufactured products meet quality standards. This means that we incorporate quality assurance systems and procedures when:
1. Purchasing and receiving starting materials
2. Producing products
3. Packaging products
The main aim of quality assurance is to identify and manage any quality issues before the product is completed and that the products we produce are fit for their intended use and they comply with registration requirements whilst ensuring that the target species are not at risk by inadequate quality, safety and efficacy.
2. QUALITY CONTROL:
Quality control refers to the sampling, testing and results in order for products to be released for sale or supply. Finished products that do not meet quality standards must not be sold or supplied.
QC responsibilities include:
Sample receipt processes
Testing of samples of starting materials, process materials and finished products
1. Testing of media fills
2. Calculating and checking results
3. Recording all results
4. Test method validation
5. Water and environment sampling and testing
6. Animal and chemical testing
3. PRODUCT QUALITY REVIEWS:
Product quality reviews aim to highlight any trends and identify product and process improvements to determine whether changes or re-validation needs to take place. It involves verification of the:
Consistency of an existing process
Appropriateness of current specifications for both starting materials and finished products
1. Batch reviews
2. Testing reviews
3. Deviation reviews
4. Change controls
5. Recalls / returns
6. GMP agreements
7. Validation activities
8. Raw materials and packaging components used in the process
4. QUALITY RISK MANAGEMENT:
Quality risk management is a systematic process for the assessment, control, communication and review of risks to the quality of the veterinary product. It can be applied both proactively and retrospectively.
Overview of the QRM process:
1. Risk assessment – risk identification, risk analysis and risk evaluation
2. Risk Control – risk reduction, risk acceptance
3. Communication of outcomes to all stakeholders
4. Risk review – review events
Pharmaceuticals products cannot be sold or supplied before Quality Assurance have certified that each production batch has been produced and controlled in accordance with approved production and control regulations.

GMPc Vietnam is recognized throughout Vietnam as the leader in providing turnkey consulting solutions for GMP-certified facility projects, including Pharmaceuticals, Cosmetics, Health supplements and Veterinary pharmaceutical. Though 12 years of development 2011 to 2023, GMPc has implemented more than 230 GMP-certified facility projects, equaling to more than 80% of market share of the field in Vietnam. Not only do domestic customers, foreign investors also choose GMPc as their consultant when investing new factories in Vietnam, such as Kyoto Biken Vaccine Factory, Nippon Chemiphar Pharmaceutical Factory, Shimizu Contractor, Kajima Contractor, etc.
Consulting services for EU GMP
Consulting services by GMPc Vietnam
GMP project consulted by GMPc Vietnam