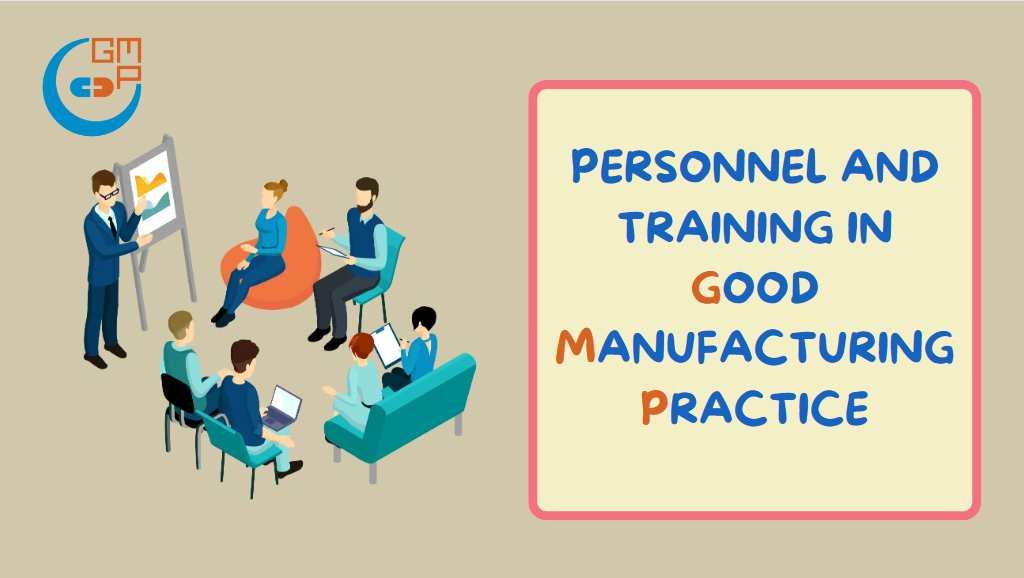
PERSONNEL AND TRAINING
The correct manufacture and quality assurance of pharmaceutical products relies upon people in the organisation. To meet the GMP requirements and ensure that everyone understands their position, role and responsibilities, the organisation has:
Organisational Charts:
The organisational charts illustrate the management and reporting structure, Quality Operations, Production and all support work areas. Staff should take some time to become familiar with these charts as they will help to understand who everyone should report any concern or incident once occurred within work area.
Written Job Descriptions:
All employees have written job descriptions which defines the position and duties of the role and limits of acability and skills required to complete the role, particularly in regard to GMP. Job Descriptions should match tasks undertaken for that role.
Extensive Training:
Training is an essential requirement and it is very important that all employees possess the right level of skills and knowledge and have the right attitude to perform their work under GMP standards.
Employees must not complete any task that they have not been trained in nor documented that training. Staff must be trained and deemed competent by their trainer with documented training records before they can perform a task unsupervised.
To ensure that all employees understand their responsibilities, the organization should provide:
1. Induction training
2. Skills training
3. GMP / GLP training to new workers
4. SOP / OI training
5. Gowning qualifications and aseptic training
6. EHS training
7. External training related to roles
8. In-house and online training
Organization must demonstrate the completion of staff training by maintaining all training records for each member of staff.
PERSONAL HYGIENE
GMP requires all employees to maintain the highest levels of personal hygiene. This means that staff must:
1. Wear protective garments correctly
2. Wash your hands thoroughly
3. Wear clean latex gloves in laboratories, production and dispensing areas
4. Not smoke, drink or eat in production and storage areas
5. Leave personal belongings outside of manufacturing areas
6. Report any illnesses, infectious diseases or open lesions
7. Follow all other hygiene practices, as outlined in the organisation’s procedure
Wear protective garments correctly:
Organization should provide its employees with personal protective garments including coveralls, gloves, hairnets, beard / moustache covers, shoe covers and safety glasses.
These garments should be worn at all times in the production areas and be removed:
1. When leaving the production area (except during an emergency, where this is not necessary).
2. When garments become wet, dirty or soiled.
Coveralls must be discarded daily and sent for laundering.
Protective clothing areas where live microorganisms are being cultured is to be decontaminated by autoclaving before being discarded or laundered.
Wash your hands thoroughly:
Hands should be thoroughly washed with soap on exiting laboratories, manufacturing areas, prior to eating, before commencing or returning to work and after:
1. Going to the toilet
2. Smoking
3. Handling food
4. Being contaminated with the product
5. Being contaminated with other contaminants
6. Cleaning and sanitation.
Organization should supply specific hand sanitiser stations at the entry and exit points of areas where controlled API materials are used and/or stored and must be used by personnel when entering and exiting these areas.
Wear clean latex gloves in laboratories, dispensing and production areas:
Clean latex gloves should be provided and must be worn in all product contact areas to protect both the employee and the product contamination. You should also avoid touching exposed products and any parts of equipment that come into contact with products.
Gloves must be disposed of and/or changed when:
1. Leaving laboratories, dispensing and production areas
2. After completing one job and starting another
3. If the gloves come in contact with product
4. If the gloves become damaged, grotty or contaminated
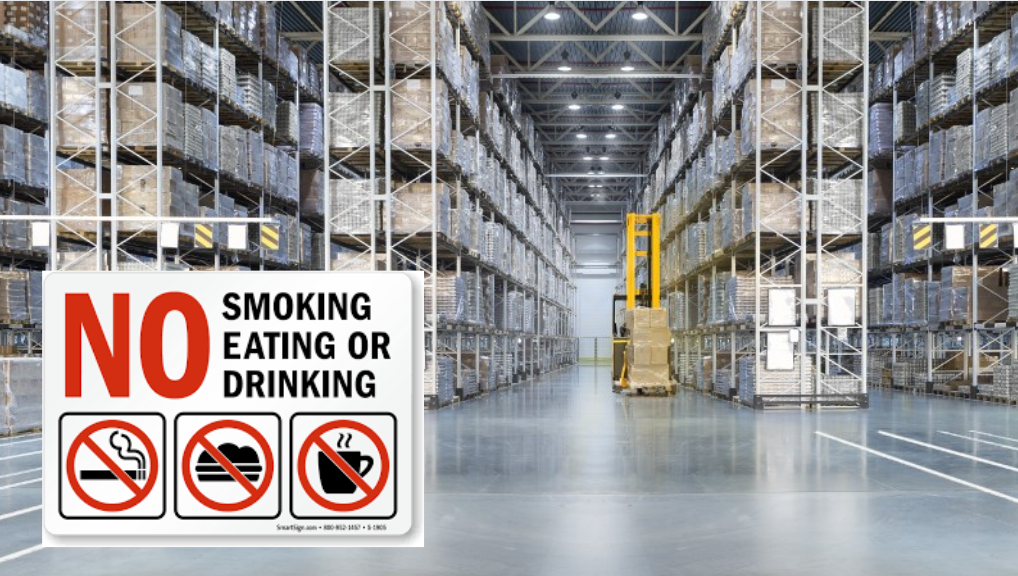
Not smoke, drink or eat in production and storage areas:
Smoking is prohibited in any area, other than the authorised designated smoking area (outside the facility).
Food (including chewing gum and lollies) and beverages must not be transported through, stored or consumed in production and storage areas.
Leave personal belongings outside of manufacturing areas:
Employees must not bring personal items into laboratories, dispensing, production and storage areas. Such items can pose a risk of cross-contaminating products. The following are examples of these items:
1. Jackets / jumpers
2. Books / magazines
3. Handbags / wallets
4. Personal medication
5. Mobile phones / pagers
6. Some jewellery
Report any illnesses, infectious diseases or open lesions:
In order to maintain product quality, employees suffering any of the following illnesses are not permitted to engage in activities where operator-borne contaminants may pose a risk to product quality. Such conditions must be reported to the area supervisor who will assign appropriate activities for the operator whilst so afflicted.
1. Coughs, cold or flu
2. Infectious diseases
3. Open lesions
4. Severe sunburn and peeling skin on an exposed surface of the body
Follow all other hygiene practices, as outlined:
All staff employed in manufacturing are required to comply with the following hygiene requirements:
1. minimising the use of jewellery and ensuring that it is securely contained under protective garments
2. wedding bands and earrings must be taped and covered
3. jewellery that may become detached or caught in machinery is prohibited in all manufacturing areas
4. make-up in all manufacturing and storage areas is prohibited
5. false nails and/or eyelashes in all manufacturing and storage areas are prohibited
6. operators must not have direct contact between their hands and exposed products or any part of equipment that comes in contact with product
7. every person (staff, visitors, maintenance, contractors) entering manufacturing areas must wear appropriate protective clothing)
8. protective clothing and factory uniforms are not to be worn outside the factory premises.
NOTE:
The wearing of wristwatches and jewellery (including earrings, studs and piercings is prohibited in aseptic processing areas.
The wearing of wristwatches and jewellery is probably permitted in packaging areas if covered by protective clothing.

GMPc Vietnam is recognized throughout Vietnam as the leader in providing turnkey consulting solutions for GMP-certified facility projects, including Pharmaceuticals, Cosmetics, Health supplements and Veterinary pharmaceutical. Though 12 years of development 2011 to 2023, GMPc has implemented more than 230 GMP-certified facility projects, equaling to more than 80% of market share of the field in Vietnam. Not only do domestic customers, foreign investors also choose GMPc as their consultant when investing new factories in Vietnam, such as Kyoto Biken Vaccine Factory, Nippon Chemiphar Pharmaceutical Factory, Shimizu Contractor, Kajima Contractor, etc.
Consulting services for EU GMP
Consulting services by GMPc Vietnam
GMP project consulted by GMPc Vietnam