What is Process Validation?
Process validation is a step-by-step procedure designed to ensure that a manufacturing process can consistently produce quality products. It is performed by a validation team led by the quality assurance head of manufacturers in the pharmaceutical industry. Generally, process validation is done before releasing a new product, when applying any change on an existing product, and for periodically verifying the process. Established at the onset, a protocol should specify how the validation process will be carried out, including the parameters to be monitored, the samples to be taken, and the results to be accepted.
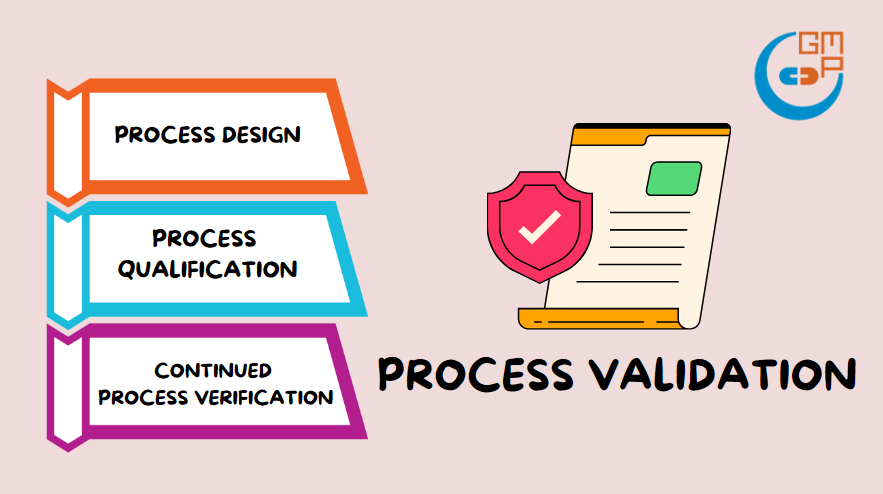
3 Stages of Process Validation
The USFDA emphasizes the collection and evaluation of data in their definition of process validation. It is crucial for the validation team not only to gather information about the activities throughout the lifecycle of the product and process, but also to analyze them for understanding the origins of variation and controlling it accordingly. The 3 stages of process validation are process design, process qualification, and continued process verification:
Stage 1: Process Design
During this stage, the manufacturing process is defined in a way that it can reproduce the delivery of a medicinal product that meets pre-determined specifications and quality attributes. To achieve this, the validation team should have a clear grasp of how the process actually works. Consider the following sources and methods to capture process information:
- Product development activities
- Functionality and limitations of production equipment
- Predicted contributions to variability
- Design of experiment (DOE) studies
- Risk analysis tools
- Experiments or demonstrations at laboratory or pilot scale
- Computer-based or virtual simulations
This stage also involves process control, planning strategies to reduce input variation and/or adjust for it during manufacturing. Controls commonly consist of material analysis and equipment monitoring at significant processing points. In some cases, the use of process analytical technology (PAT) may be needed.
Stage 2: Process Qualification
The process qualification stage of process validation entails process design evaluation to determine if it is effective for quality production. First, the manufacturing facility should be designed according to the requirements of current good manufacturing practice (CGMP). Next, qualification of utilities and equipment should be conducted such as making sure that they are built and installed in compliance with design specifications. Finally, process performance qualification should be executed through a protocol and documented in a report:
- Introduction, Objectives, and Scope
- Production, Quality Assurance (QA), and Quality Control (QC) Responsibilities and Prerequisites (e.g. manufacturing records)
- Process Validation Study Plan based on Quality Risk Management (QRM)
- Validation Team (Research and Development, Engineering, Production, QA, and QC)
- Product Details and Design Considerations
- List of Materials, Vendors, and Master Formula
- List of Equipment and Process Flow Chart
- Brief Manufacturing Process and Assessment of Critical Process Parameters (CPP)
- In-process Test and Specifications or Critical Quality Attributes (CQA)
- Sampling, Testing Plan, and Acceptance Criteria and Limit
- Yield Details (a minimum of three consecutive batches)
- Analytical Method Validation
- Finished Product Specification
- Review of Out-of-Specification (OOS) Test Results, Deviation, and Change Control (CC)
- Revalidation Criteria
- Review of Follow-up Action (if any)
- Summary and Conclusion
Stage 3: Continued Process Verification
After process design and process qualification, the third stage of process validation deals with setting systems to continually ensure that the validated process remains in such a state during routine production. Continued process verification often incorporates the use of statistical process control (SPC), the continuous monitoring and sampling of process parameters and quality attributes, and the scheduled maintenance of the facility, utilities, equipment, and related assets. It is essential for good documentation practices to be employed throughout the validation process.

GMPc Vietnam is recognized throughout Vietnam as the leader in providing turnkey consulting solutions for GMP-certified facility projects, including Pharmaceuticals, Cosmetics, Health supplements and Veterinary pharmaceutical. Though 12 years of development 2011 to 2023, GMPc has implemented more than 230 GMP-certified facility projects, equaling to more than 80% of market share of the field in Vietnam. Not only do domestic customers, foreign investors also choose GMPc as their consultant when investing new factories in Vietnam, such as Kyoto Biken Vaccine Factory, Nippon Chemiphar Pharmaceutical Factory, Shimizu Contractor, Kajima Contractor, etc.
Consulting services for EU GMP
Consulting services by GMPc Vietnam
GMP project consulted by GMPc Vietnam