Good Manufacturing Practices (GMP) focuses on five key elements, often referred to as the 5 Ps of GMP to ensure that organizations comply with strict standards throughout the entire production process.
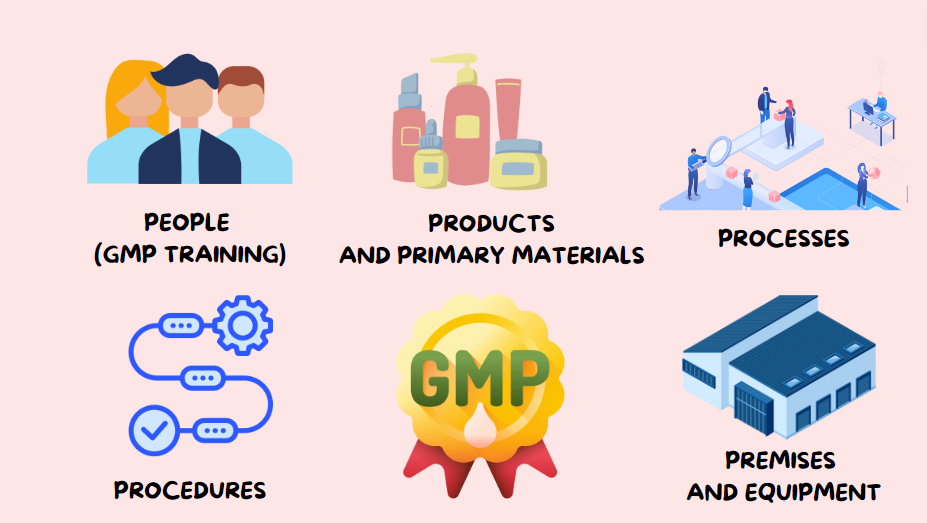
The 5 Pillars of Good Manufacturing Practices are:
People (GMP Training)
All manufacturing facilities must strictly adhere to GMPs and all employees must strictly follow manufacturing processes and regulations. This cannot be done without proper GMP training because providing compliance training to staff is the best way to ensure compliance with GMP standards. All employees involved in the drug manufacturing process must undergo GMP training to fully understand their roles and responsibilities. In addition, their performance must be evaluated as well as the training methods which must be continuously reviewed so that the manufacturer can ensure that its employees are well trained and competent.
Procedures
GMPs hold manufacturers acable by requiring that procedures be documented and recorded. A procedure is a set of guidelines for undertaking critical processes such as pharmacovigilance, cold chain, batch recalls, etc. to achieve a consistent outcome. It must be presented to all employees, and training must be provided if necessary. Any form of deviation the procedure must be analyzed and reported.
Products and Primary Materials
All products must undergo constant testing, comparison, and quality assurance before being released to consumers. Additionally, the raw materials used in the formulas must have precise specifications at each stage of manufacture, and there must be a record of the master formula. Standard methods should be followed for product packaging, testing, and sampling. Finally, test results must be recorded so that manufacturers are continually prepared for internal or external audits of their products.
Processes
It is part of the requirement that each process is clearly defined, correctly documented, consistent, distributed to all employees, and evaluated. Indeed, a regular evaluation must be carried out to ensure that all operations comply with current processes and meet the required standards. The manufacturer must have clear visibility of the operations. Compliance must be demonstrable by an auditor at any time and available for self-inspection to facilitate any possible improvement, as continuous improvement is a principle that drives GMPs.
Premises and equipment
In pharmaceutical manufacturing, premises include what lies beyond the walls of the facility. This is because there are regulations for the surrounding area to follow, including water systems and waste disposal. That being said, the premises involve all the infrastructure and systems around cleanliness to avoid cross-contamination, accidents, or even fatalities. All equipment should be placed or stored correctly and continuously validated and calibrated to ensure it is suitable to produce consistent results to prevent the risk of equipment failure. In addition, there must be clear procedures and documents for cleaning premises and equipment.
Consumers expect every batch of drugs they take to meet quality standards so that they are safe and effective. GMPs contain all the guidelines for organizations to meet this expectation throughout the manufacturing process. Today, there are new technologies for business operations that allow manufacturers to guarantee the public trust in the manufacturing quality of medicines. More and more organizations are relying on digital solutions to run their business, and that's the way to go if they want to compete in this industry in today's market.

GMPc Vietnam is recognized throughout Vietnam as the leader in providing turnkey consulting solutions for GMP-certified facility projects, including Pharmaceuticals, Cosmetics, Health supplements and Veterinary pharmaceutical. Though 12 years of development 2011 to 2023, GMPc has implemented more than 230 GMP-certified facility projects, equaling to more than 80% of market share of the field in Vietnam. Not only do domestic customers, foreign investors also choose GMPc as their consultant when investing new factories in Vietnam, such as Kyoto Biken Vaccine Factory, Nippon Chemiphar Pharmaceutical Factory, Shimizu Contractor, Kajima Contractor, etc.
Consulting services for EU GMP
Consulting services by GMPc Vietnam
GMP project consulted by GMPc Vietnam