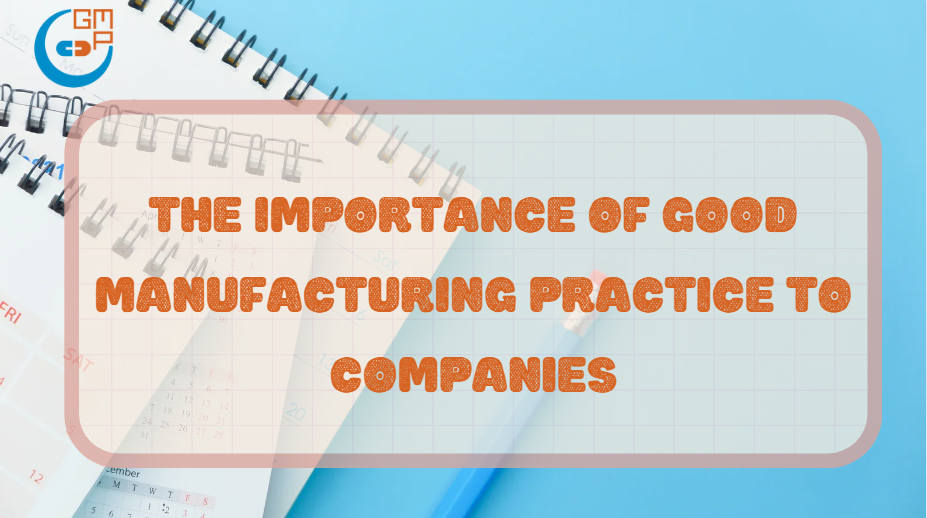
Good Manufacturing Practice (GMP) guidelines aid manufacturers in improving their production of goods. GMP ensures that companies execute consistent procedures within safe environments. Hence, it prevents contamination, recalls, and loss of profit.
GMP comes with strict protocols that lessen the risk of manufacturing errors. In the same way, companies can sustain efficient systems and processes to produce safe goods.
A Quick Recap on GMP
A Good Manufacturing Practice (GMP) is a scheme that ensures products are manufactured and controlled according to quality standards.
These standards apply to the production of:
GMP covers every part of the manufacturing process to prevent risks such as mislabeling and contamination.
Note that rules and interpretations may differ ry to ry. Hence, knowing the basis of GMP is important.
Purpose of Good Manufacturing Practices: Why is GMP Relevant?
In general, consumers cannot fully detect whether food, drugs or cosmetic products are safe. They are putting a huge trust in manufacturers about the effectivity of goods they are buying.
Manufacturers must initiate testing out products to attain quality. Applying Good Manufacturing Practice at various levels of production can help assure quality.
Furthermore, companies must apply regulations or guidelines for every facility, equipment, and process for the design and production of goods.
By following GMP standards, companies meet the best systems to produce safe and effective goods.
Prevent Damage to Health
Manufacturers that don’t apply GMP may produce poor quality pharmaceutical goods. In some cases, the production process may unintentionally add toxic substances to medicines.
In effect, consumers won’t be able to receive the therapeutic effect they are paying for. Worse, they may experience negative impacts on health.
Avoid Harmful Skin Conditions
Good Manufacturing Practice guidelines aim to prevent finished cosmetic products harming customers.
Consumers apply make-up and perfume on their skin, so ingredients must not be damaging.
Defined and Controlled Hygiene Protocols
Keep in mind that consumers will eat food, drink beverages, and take in medicines. Your products can have an immediate effect on a person’s body.
Processes that follow GMP make sure employees have the appropriate gear as well as training on hygiene protocols.
Facilities with hygienic employees and clean manufacturing areas prevent cross-contamination.
Improved Processes and Production Environment
Good Manufacturing Practices maintain facilities in good condition. In this way, employees can preserve good clinical practice.
As a result, companies can continuously train their staff. GMP also aids manufacturers in making sure they have qualified, validated, and verified equipment.
In addition, these measures result in calibrated and accurate measurements. Consequently, manufacturers who use GMP can maintain consistent and reproducible processes.
Cut Profit Loss
Poor quality goods are a waste of money for manufacturers, consumers, and governments.
Some governments allocate budget for free or subsidized medicines for their citizens. Hence, they will invest large sums of money on pharmaceutical companies.
Individual consumers also invest at least a monthly budget on medicines, especially if doctors give them prescription drugs.
For manufacturers, they invest time, money, and resources in production.
Another benefit of implementing GMP is that it can help cut down waste, and subsequently, loss of money.
Ensuring all parties are safe negative safety cases can avoid profit loss as well.
Lessen Complains and Avoid Recalls
Poorly produced goods can create a bad image for your company. In some cases, it could even harm your credibility as a manufacturer.
Customer complaints add unnecessary manpower. Your company would also need to designate a team to manage potential recall as well as refunds.
However, goods produced under GMP are less likely to end up in a recall. In fact, consumers are more likely to give good reviews.
Boost Export Opportunities
Some ries and importers use internationally recognized Good Manufacturing Practices as a basis for buying foreign medicines and cosmetics.
Thus, governments who want to promote their ries’ export must make GMP mandatory.
In relation, they must train inspectors to assess GMP requirements.
Schedule GMP Audits
One of the benefits of Good Manufacturing Practices is that your company can conduct GMP auditing. In this manner, you can secure that premises, employees, materials, and procedures still comply with the GMP guidelines.
The audit gives you a clearer picture of your company’s current status in GMP compliance. In the same way, you can observe what areas to improve.
Operational Procedures to Fulfill GMP Requirements
- Proper layout, construction, and external environment of the food premises.
- Cleanliness of premises, floors, walls, ceilings, equipment, and utensils.
- Thorough maintenance of all equipment, utensils, and storage.
- Use of suitable chemicals such as machine lubricants and cleaning substances.
- Avoiding foreign matter such as plastic, glass, wood, metal, paper, string, tape, and pests within the finished product.
- Implementation of a pest control program within the premises and surrounds.
- Organization and storage of waste.
Aspects of Good Manufacturing Practice Compliance
Meeting GMP regulations means performing different processes. The good thing is that every process is a step to ensuring quality products.
Optimizing easy-to-use scheme and robust processes can strengthen GMP compliance in your company.
- Using in-process control to improve quality
- Better compliance through master manufacturing records
- Supplier and vendor qualification
- Improving documentation of GMP procedures, batch production records, and deviations
- Equipment and facility design
- Packaging and labeling
- Testing
- Complaints and recalls
- Training documentation
The Necessity of Good Manufacturing Practices
With the help of GMP, companies can develop a proactive workforce that can continuously improve their production of quality goods.

GMPc Vietnam is recognized throughout Vietnam as the leader in providing turnkey consulting solutions for GMP-certified facility projects, including Pharmaceuticals, Cosmetics, Health supplements and Veterinary pharmaceutical. Though 12 years of development 2011 to 2023, GMPc has implemented more than 230 GMP-certified facility projects, equaling to more than 80% of market share of the field in Vietnam. Not only do domestic customers, foreign investors also choose GMPc as their consultant when investing new factories in Vietnam, such as Kyoto Biken Vaccine Factory, Nippon Chemiphar Pharmaceutical Factory, Shimizu Contractor, Kajima Contractor, etc.
Consulting services for EU GMP
Consulting services by GMPc Vietnam
GMP project consulted by GMPc Vietnam