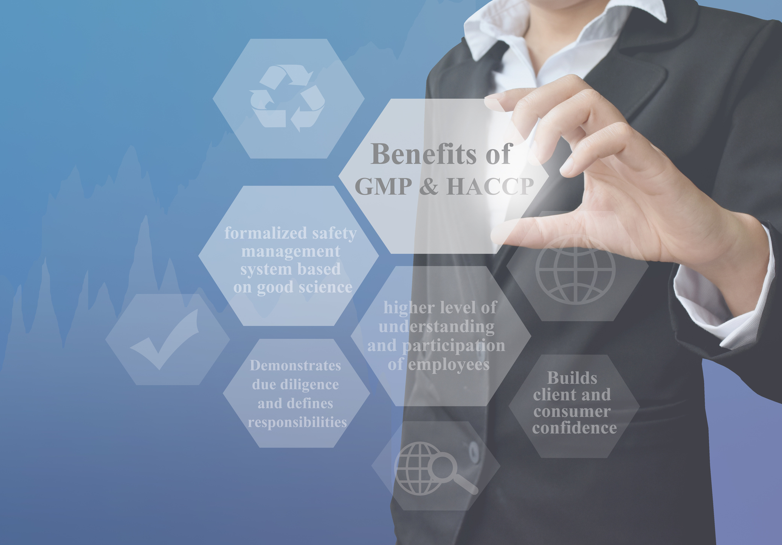
Quality assurance in the pharmaceutical industry
Quality Assurance (QA) is a broad concept that covers all the most important aspects of the entire drug manufacturing process. It is a process performance and product quality monitoring system that helps companies protect their image and avoid penalties regulators. But beyond that, it ensures that the prescribed drug produces the desired effect and ensures that the drugs comply with the regulations.
It should be noted that if a manufacturer fails to meet pharmaceutical grade standards, they may not only face hefty fines, but also possible legal actions that can jeopardize their business. This is why anyone involved in the manufacturing process must receive specific pharmaceutical training.
Pharmaceutical companies associate QA with the eight pillars of the Pharmaceutical Quality Systems (PQS) to provide high-quality finished pharmaceutical products. Those 8 pillars consist of: Auditing, QMS consultancy and design, GMP compliance, Training, Standard Operating Procedures (SOP) development, Qualified Person and Responsible Person provision, Inspection preparation and support, and Quality risk management.
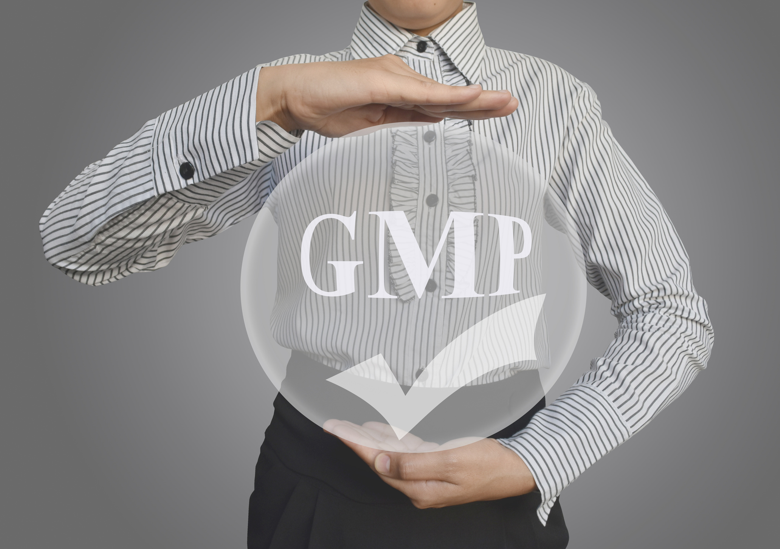
What are Good Manufacturing Practices (GMPs)?
According to the World Health Organization, good manufacturing practice (GMP) is a system for ensuring that products are consistently produced and controlled according to quality standards.
Good Manufacturing Practices (GMP) is a compilation of various guidelines, guidance documents, directives issued and developed by international organizations and institutions, in collaboration with the pharmaceutical industry and several national regulatory authorities in different regions and ries, to ensure the highest standards of efficiency, quality and safety in any process involving the manufacture of pharmaceutical products. Most ries have legislated for manufacturers to follow GMP procedures.
It is a system that consists of processes, procedures, and documentation that ensures manufacturing products are consistently produced and controlled according to the set of quality standards. guidelines guide manufacturing, testing, and quality assurance to ensure that a manufactured product is safe for human consumption or use.
GMP guarantees pharmaceutical manufacturers’ reputation, reduces risk, helps companies save money (batch recall, lawsuit compensations, fines, etc.), and create a competitive edge in an increasingly crowded and competitive marketplace.
An important distinction to mention is that between good manufacturing practices (GMP) and current good manufacturing practices (cGMP). Usually interchangeable, GMP is the basic regulation published by the Food and Drug Administration (FDA) under the authority of the Federal Food, Drug, and Cosmetic Act to ensure that manufacturers take all necessary measures to ensure that their products are safe and effective. cGMP, on the other hand, has been implemented by the FDA to ensure continuous improvement in manufacturers' approach to product quality (constant commitment to the highest quality standards, use of new systems and technologies, …)

GMPc Vietnam is recognized throughout Vietnam as the leader in providing turnkey consulting solutions for GMP-certified facility projects, including Pharmaceuticals, Cosmetics, Health supplements and Veterinary pharmaceutical. Though 12 years of development 2011 to 2023, GMPc has implemented more than 230 GMP-certified facility projects, equaling to more than 80% of market share of the field in Vietnam. Not only do domestic customers, foreign investors also choose GMPc as their consultant when investing new factories in Vietnam, such as Kyoto Biken Vaccine Factory, Nippon Chemiphar Pharmaceutical Factory, Shimizu Contractor, Kajima Contractor, etc.
Consulting services for EU GMP
Consulting services by GMPc Vietnam
GMP project consulted by GMPc Vietnam